Instandhaltung: Budgetplanung
Facility Management: Instandhaltung » Abläufe » Strategische Planungsprozesse » Budgetplanung
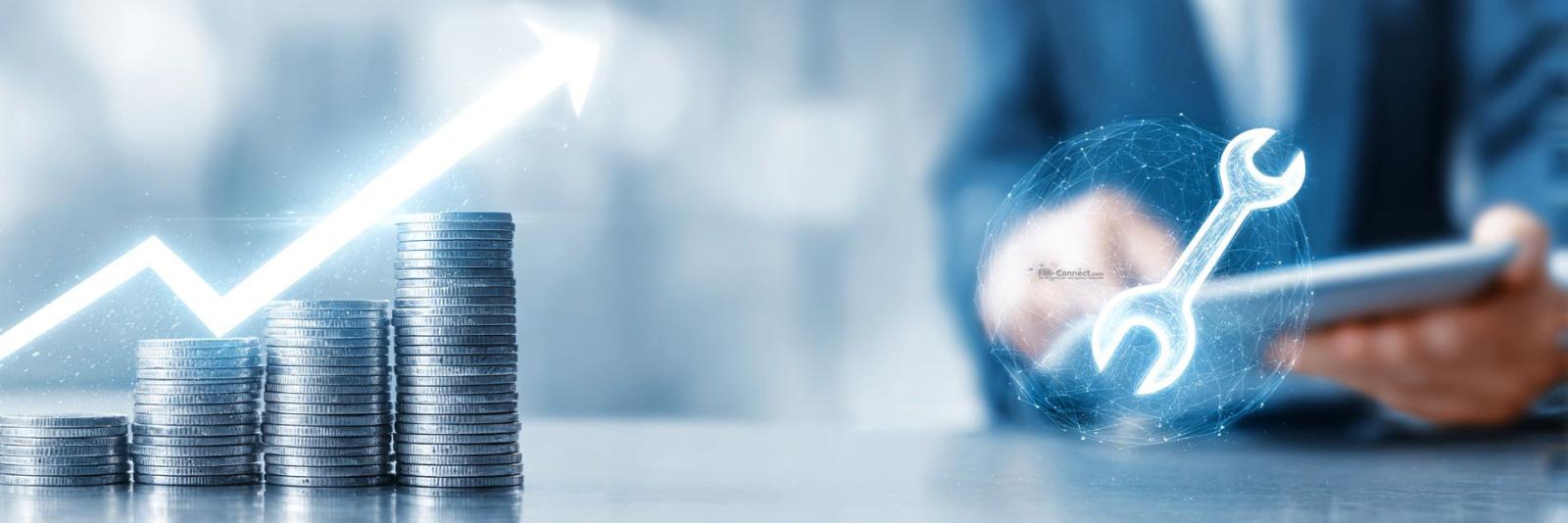
Praxisorientierte Budgetplanung für die Instandhaltung
Die Instandhaltung technischer Anlagen ist ein entscheidender Faktor für die Produktionssicherheit und Wertschöpfung. Eine systematische Budgetplanung der Instandhaltung verbindet diese Kosten eng mit der Instandhaltungsplanung, damit notwendige Maßnahmen finanziell hinterlegt und kontrolliert durchgeführt werden können. Ziel einer methodisch fundierten Budgetierung ist es, den optimalen Instandhaltungsaufwand zu bestimmen: Genügend Budget einzuplanen, um die Anlagen zuverlässig zu betreiben, ohne Ressourcen durch übermäßige Maßnahmen zu verschwenden. Dieser Balancepunkt liegt dort, wo die Summe aus Instandhaltungs- und Ausfallkosten minimal ist. Technische Kenntnisse über Anlagenzustände und Wartungsbedarfe müssen mit betriebswirtschaftlichen Methoden der Kostenanalyse und -prognose verknüpft werden. Durch die strukturierte Vorgehensweise – von der gründlichen Datensammlung über Pivot-gestützte Analysen nach technischen Dimensionen bis hin zur mehrjährigen Prognose unter Berücksichtigung von Alter, Nutzung und präventiven Maßnahmen – entsteht ein fundiertes Budget, das sowohl realistisch als auch strategisch ausgerichtet ist. Entscheidend ist, dass das Budget nicht als starre Begrenzung gesehen wird, sondern als Steuerungsinstrument. Im Planungsprozess werden wertvolle Insights gewonnen (z. B. welche Anlagen besonders kostentreibend oder störanfällig sind), die direkt in Verbesserungsmaßnahmen einfließen können. Eine zuverlässige, gut gepflegte Anlage produziert qualitativ einwandfrei und ohne ungeplante Unterbrechungen – dafür bildet das Instandhaltungsbudget den finanziellen Rahmen, den es mit Sachverstand zu ermitteln und verantwortungsvoll einzusetzen gilt.
Grundlagen: Instandhaltungsplanung und Kostenfaktoren
Eine fundierte Budgetplanung setzt Verständnis der Instandhaltungsstrategien und Kostenstruktur voraus. Grundsätzlich unterscheidet man reaktive Instandhaltung (Reparaturen nach Ausfall) und präventive Instandhaltung (geplante Wartung zur Vermeidung von Ausfällen). Präventive, produktive Instandhaltung zielt darauf ab, durch regelmäßige Wartung und Inspektion die Anlagenverfügbarkeit zu maximieren und ungeplante Stillstände zu minimieren. Zwar können häufige Wartungszyklen die meisten Ausfälle verhindern, jedoch sind auch Wartungsmaßnahmen selbst mit direkten Kosten und Stillstandszeiten verbunden. Es gilt also, einen sinnvollen Kompromiss zwischen Instandhaltungskosten und Ausfallfolgekosten zu finden. Abbildung 1 veranschaulicht diesen Zusammenhang qualitativ: Mit steigender Wartungsintensität nehmen die direkten Instandhaltungskosten (pink) zu, während gleichzeitig die Ausfallkosten (grün) infolge ungeplanter Stillstände abnehmen; die Summe beider Kostenelemente (blau) zeigt ein Minimum, das den optimalen Wartungsaufwand markiert. Neben der Wartungsstrategie beeinflussen technische und betriebliche Faktoren die Instandhaltungskosten. Hierzu zählen vor allem: Anlagenalter, Nutzung, Hersteller/Produkt sowie Einsatzbedingungen. Ältere Anlagen verursachen tendenziell höhere Wartungs- und Reparaturaufwände, da Verschleiß über die Zeit zunimmt und Ersatzteile schwieriger verfügbar werden. Ebenso steigt bei intensiv genutzten Maschinen (hohe Betriebsstunden oder Auslastung) der Wartungsbedarf überproportional an, etwa durch erhöhten Verschleiß und häufigere Inspektionen. Der Zustand der Anlage spielt eine große Rolle: Gut gewartete und gepflegte Anlagen in einem ordentlichen Zustand zeigen höhere Zuverlässigkeit, wohingegen vernachlässigte oder abgenutzte Anlagen vermehrt Störungen aufweisen. Die Umgebungseinflüsse (z. B. Staub, Feuchtigkeit, Temperaturextreme) können ebenfalls die Instandhaltungskosten treiben, da sie bestimmte Schäden begünstigen und kürzere Wartungsintervalle erfordern. Schließlich können Unterschiede zwischen Herstellern und Bauarten relevant sein – manche Fabrikate gelten als wartungsarm und langlebig, während andere häufiger ausfallen oder teurere Ersatzteile benötigen. Ein Ziel des Instandhaltungscontrollings ist es daher, Fragen wie „Welcher Hersteller fällt immer wieder aus?“ beantworten zu können. Durch eine strukturierte Datenauswertung lassen sich besonders ausfallanfällige Fabrikate oder Modellreihen identifizieren, was in die Budgetplanung (etwa durch höhere Ersatzteilkosten oder präventive Austauschaktionen) einfließt.
Bei all diesen Vergleichsmöglichkeiten ist jedoch Vorsicht geboten: Unterschiedliche Anlagentypen oder Aggregate lassen sich nicht unmittelbar in ihren Kosten vergleichen. Komplexe, große Anlagen werden naturgemäß höhere Instandhaltungsaufwände haben als einfache, kleine Maschinen. Selbst innerhalb einer Kategorie können technische Unterschiede (z. B. eine modifizierte Anlage oder verschiedene Baujahre) den Vergleich verzerren. In der Praxis zeigt sich häufig, dass selbst bei ähnlichem Alter und gleicher Funktion keine vollständig vergleichbaren Anlagen vorliegen – etwa weil Umbauten vorgenommen wurden oder eine Anlage technologisch überholt ist. Daher sollte die Budgetanalyse immer strukturierend gruppiert erfolgen (z. B. nach Anlagenklassen), um möglichst homogene Vergleichsgruppen zu bilden. Unterschiede zwischen den Gruppen – etwa Pumpen versus Förderbänder – sind erwartbar und nicht als Effizienzabweichung fehlzuinterpretieren.
Ein weiterer wichtiger Aspekt der Grundlagen ist das Konzept der direkten und indirekten Instandhaltungskosten. Direkte Instandhaltungskosten sind unmittelbar den Maßnahmen zuordenbar – typischerweise Personalaufwand interner Techniker, Material- und Ersatzteilkosten sowie Kosten externer Service-Dienstleister. Indirekte Kosten dagegen entstehen durch die Folgen von Anlagenmängeln oder Ausfällen: Produktionsausfall und entgangener Umsatz, Qualitätsminderungen und Ausschuss, Terminverzögerungen mit eventuellen Vertragsstrafen, erhöhte Energieverbräuche bei ineffizientem Betrieb, oder auch Sicherheitsrisiken und Unfälle. Diese indirekten Kosten werden bei einer rein technischen Budgetbetrachtung oft übersehen. Studien zeigen, dass über 95 % der kleineren und mittleren Unternehmen (KMU) ihre indirekten Instandhaltungskosten nicht beziffern können – ein wichtiger blinder Fleck. Für eine realistische Budgetplanung muss jedoch auch der wirtschaftliche Nutzen präventiver Instandhaltung berücksichtigt werden: Vorbeugende Maßnahmen mögen die direkten Kosten erhöhen, vermeiden aber potentielle hohe Ausfallkosten und bewahren die Wertschöpfung. So können frühzeitige Inspektionen und Wartungen erhebliche Einsparungen ermöglichen, indem zeitaufwändige Reparaturen oder Folgeschäden gar nicht erst auftreten. In der Gesamtbetrachtung führt eine produktive, vorbeugende Instandhaltung daher meist zu einem günstigeren Verhältnis von Aufwand und Ertrag – sie ist kein reiner Kostenfaktor, sondern ein Wertfaktor für das Unternehmen.
Methodik der Budgetplanung
Die Budgetplanung für die Instandhaltung folgt einem mehrstufigen Prozess, der sowohl vergangenheitsbasierte Datenanalyse als auch zukunftsgerichtete Prognosen umfasst.
Im Folgenden wird ein systematisches Vorgehen beschrieben, das sich in der Praxis bewährt hat:
Datenerfassung und -aufbereitung: Zunächst werden alle relevanten Ist-Kosten der Instandhaltung aus vergangenen Perioden gesammelt. Typischerweise umfasst dies die letzten 2–5 Jahre als Basis für Trends. Moderne Instandhaltungsorganisationen nutzen hierfür ERP-Systeme wie SAP PM/EAM (Plant Maintenance/Enterprise Asset Management). SAP-Technische Plätze (Funktionsstandorte) und Instandhaltungsobjekte (Equipments) dienen als Strukturelemente, an denen Aufträge und Kosten verbucht werden. Es ist wichtig, die Kosten pro technischem Objekt eindeutig zuordnen zu können (z. B. durch Angabe des Equipmentnummer oder technischen Platzes auf jedem Instandhaltungsauftrag). Zudem sollten Stammdaten wie Anlagenklasse, Hersteller, Baujahr, Leistungsdaten etc. für jedes Objekt verfügbar sein – etwa über Klassifizierung (sogenannte F-Klassen für Funktionsklassen bzw. Anlagenkategorien). Datenqualität hat in dieser Phase oberste Priorität: Alle historischen Kostenwerte müssen bereinigt und validiert werden. Praktisch bedeutet das, Dopplungen oder Fehlbuchungen zu korrigieren und sicherzustellen, dass Instandhaltungskosten nicht in anderen Budgets „versteckt“ wurden. Häufig zeigt sich z. B., dass kleinere Wartungen von der Produktion mit übernommen und nicht auf Instandhaltungskonten verbucht wurden. Ebenso werden entnommene Ersatzteile oder interne Personalkosten manchmal nicht den richtigen Kostenträgern (Anlagen) zugerechnet. Solche Unschärfen führen zu einer Verzerrung der historischen Kostendaten und damit zu falschen Kalkulationsgrundlagen. „Wer seine vorhandenen Daten korrekt nutzt, kann seine Kosten für die Instandhaltung genauer budgetieren.“ – dieses Zitat aus der Fachliteratur verdeutlicht, dass erst nach sorgfältiger Datenaufbereitung eine präzise Budgetplanung möglich ist. Im Zweifelsfall sollte man lieber konservativ unbekannte Kostenreserven berücksichtigen, um nicht durch scheinbar niedrige Vorjahreswerte in trügerischer Sicherheit zu wiegen.
Analyse der historischen Instandhaltungskosten: Auf Basis der bereinigten Daten erfolgt eine detaillierte Analyse der Ist-Kosten. Hier hat es sich bewährt, mit Pivot-Auswertungen oder Business-Intelligence-Tools (z. B. SAP BW, Excel-Pivot) die Daten in verschiedenen Dimensionen zu betrachten. Zentrale Auswertungskriterien sind: Technisches Objekt, Standort, Anlagenklasse (F-Klasse), Kostenart sowie Zeit (Jahr, Quartal). Durch die Pivot-Analyse erhält die Instandhaltungsleitung einen schnellen Überblick über Kostentreiber und Ausreißer. Beispielsweise kann man die Gesamtkosten der letzten Jahre pro Anlage/Equipment auflisten und so die teuersten Betriebsmittel identifizieren. Ebenso lässt sich ein standortübergreifender Vergleich durchführen: Wie hoch waren die Instandhaltungskosten Werk A vs. Werk B pro Jahr insgesamt und heruntergebrochen nach Anlageklassen? Tabelle 1 demonstriert eine mögliche Gegenüberstellung nach Standort und Klassen. Solche Tabellen schaffen Transparenz und ermöglichen es, Auffälligkeiten zu erkennen – etwa wenn an Standort B die Kosten für eine bestimmte Anlagenklasse deutlich höher liegen als an Standort A.
Anlagenklasse (F-Klasse) | Kosten Werk A (2024) | Kosten Werk B (2024) | Differenz A vs. B |
---|---|---|---|
F1: Pumpen und Motoren | 500 T € | 620 T € | +24% |
F2: Fördertechnik (Bänder) | 300 T € | 290 T € | –3% |
F3: Wärmebehandlungsöfen | 450 T € | 510 T € | +13% |
F4: Sonstige Anlagen | 200 T € | 210 T € | +5% |
Gesamt | 1.450 T € | 1.630 T € | +12% |
Neben der aggregierten Sicht werden bei der Analyse auch die Kosten pro technischem Platz/Objekt untersucht. Hierzu werden alle Kosten, die einem Equipment bzw. Funktionsplatz zugeordnet sind, über die Zeit summiert. Oft zeigt sich eine Pareto-Verteilung: eine kleine Anzahl von Anlagen verursacht einen Großteil der Kosten. Diese Top-Kostentreiber gilt es näher zu beleuchten. Mögliche Ursachen können sein: besonderes Alter oder Verschleißzustand, Konstruktionsmängel, falsche Bedienung, unzureichende Wartungshistorie oder einfach die kritische Bedeutung (und damit intensive Nutzung) der Anlage. Durch Zeitreihenanalyse der einzelnen Objekte (z. B. jährliche Kostentrends) erkennt man auch, ob die Aufwände steigen – ein potenzieller Hinweis auf Alterungs- oder Abnutzungserscheinungen – oder ob sie unregelmäßig sprunghaft sind (was auf sporadische Großreparaturen hindeutet). Ein essentieller Schritt in der Analyse ist die Ausreißeranalyse. Dabei werden außergewöhnliche Kostenvorkommnisse identifiziert, etwa ein einzelnes Jahr mit extrem hohen Reparaturkosten aufgrund eines Großschadens oder einer umfassenden Generalüberholung. Solche Ausreißer sollten isoliert betrachtet werden: Man markiert sie als außerordentliche Instandhaltungskosten und entscheidet, wie sie für die Zukunft zu behandeln sind. Beispielsweise kann ein einmaliger Großschaden nicht jedes Jahr im Budget veranschlagt werden; allerdings ist zu prüfen, ob daraus rückkehrende Muster entstehen (z. B. alle 5 Jahre eine größere Überholung nötig). Ggf. teilt man historische Kosten in ordentliche (wiederkehrende) Instandhaltungskosten und außerordentliche auf. Die ordentlichen Kosten bilden den Basislauf, der typischerweise mit dem Alter und der Nutzung der Anlage langsam ansteigt. Die außerordentlichen Kosten kann man gesondert mitteln oder gezielt in dem Jahr einplanen, in dem ein ähnliches Ereignis erwartet wird (z. B. nächster geplanter Tausch eines Großaggregats). Während der Analyse-Phase werden auch Zusammenhänge und Einflussfaktoren geprüft: Gibt es Korrelationen zwischen Anlagenalter und Kostenhöhe? Sind bestimmte Hersteller in der Wartung teurer (vgl. obige Frage nach dem Herstellerausfall)? Wie wirken sich unterschiedliche Produktionsvolumina auf die Wartungskosten aus (Stichwort: Kosten pro Laufzeitstunde oder pro produzierter Einheit)? Diese Fragen führen zu Kennzahlen wie Instandhaltungskosten pro Betriebsstunde, Kosten pro Produktionseinheit oder pro € Anlagenwert. Solche Kennzahlen erlauben einen relativierten Vergleich, der unterschiedlich große oder ausgelastete Standorte und Anlagenklassen fairer gegenüberstellt. Beispielsweise könnte Werk B in Tabelle 1 zwar absolut höhere Kosten haben, aber wenn Werk B auch deutlich mehr Produktionsstunden geleistet hat, relativiert sich der Vergleich. Daher sollten Dimensionskriterien wie Auslastung, Anlagenwert oder Produktionsmenge als zusätzliche Datenebenen herangezogen werden, um die Kosten strukturiert zu analysieren.
Kostenprognose und Budgetaufstellung:
Aufbauend auf der historischen Analyse wird nun die mittelfristige Kostenprognose erstellt – üblicherweise für einen Planungszeitraum von z. B. 3–5 Jahren. Dieser Schritt verbindet trendbasierte Hochrechnungen mit konkreten Planwerten aus der Instandhaltungsplanung. Zunächst wird der Basis-Trend der ordentlichen Instandhaltungskosten je Anlage ermittelt.
Hier kann man verschiedene Prognosemethoden anwenden, etwa:
Fortschreibung des Durchschnitts: Aus den letzten z. B. 3 Jahren wird ein Durchschnittswert (ggf. indexiert mit einem Inflations- oder Preissteigerungsfaktor) als künftiger Jahresaufwand angesetzt.
Lineare Trendextrapolation: Wenn ein klarer Anstiegstrend erkennbar ist (z. B. wegen Anlagenalter), wird dieser linear (oder mit passender Trendkurve) fortgeschrieben.
Rechnerische Modelle: Für Anlagen mit mengenabhängigem Verschleiß kann ein proportionaler Anteil pro Nutzungsmenge kalkuliert werden (z. B. Wartungskosten pro 1000 Betriebsstunden oder pro produzierte Mengeneinheit). Kombiniert mit einer Prognose der Nutzung (geplante Produktionsmenge) ergibt das die variable Kostenschätzung. Hinzu kommt ein fixer Grundaufwand pro Anlage und Jahr (Basiswartung).
Des Weiteren fließen die geplanten Instandhaltungsmaßnahmen aus der Wartungsplanung in die Budgetaufstellung ein. Die Instandhaltungsplanung gibt vor, wann welche präventiven Maßnahmen stattfinden sollen – etwa größere Revisionen, die alle X Jahre anstehen, oder der routinemäßige Austausch von Verschleißteilen nach Herstellerempfehlung. Solche Maßnahmen werden terminlich zugeordnet und mit Kostenschätzungen versehen. Beispielsweise kann im zweiten Planungsjahr für eine bestimmte Maschine eine Generalüberholung (mit geschätzten Kosten Y) vorgesehen sein – diese wird gezielt in das Budget des entsprechenden Jahres eingearbeitet. Hier zahlt sich eine akkurate Vergangenheitsauswertung aus: hat man z. B. bereits Vergleichswerte einer ähnlichen Überholung in der Vergangenheit, sollten diese herangezogen werden.
Alterseffekte auf die Kosten werden ebenfalls berücksichtigt:
Für sehr junge Anlagen kann man anfangs niedrigere Instandhaltungskosten ansetzen (Garantiephase, geringerer Verschleiß). Ab einer gewissen Nutzungsdauer steigen die Aufwandposten dann an – manche Unternehmen kalkulieren hier mit prozentualen Ansätzen vom Wiederbeschaffungswert der Anlage in Abhängigkeit vom Alter. Beispielsweise könnten Instandhaltungskosten im Durchschnitt 3 % des Neuwerts pro Jahr betragen, bei älteren Anlagen aber 5–6 %. Solche Daumenwerte sollten jedoch mit tatsächlichen historischen Quoten validiert werden, da sie je nach Branche und Instandhaltungsstrategie variieren. Die Planung sollte zudem geplante Anlagenneuerungen einbeziehen: Falls im Horizont z. B. für 2026 die Anschaffung einer neuen Maschine vorgesehen ist, reduziert sich ab dann das Budget für das alte Gerät (ggf. entfallen Reparaturen, und für das neue Gerät sind nur Wartung nach Wartungsplan und Gewährleistungsansprüche relevant). Nachdem alle Einzelpositionen – Basisfortschreibung, präventive Maßnahmen, eventuelle Sondereffekte – je Anlage und Jahr geplant sind, werden diese zum Instandhaltungsbudget pro Jahr und Standort aggregiert. Hierbei erfolgt üblicherweise eine Kontrollrunde: Das errechnete Budget wird mit übergeordneten Erfahrungen und Zielen abgeglichen. Dabei können Controlling-Vorgaben ins Spiel kommen, z. B. globale Kostenziele (etwa „Instandhaltungskosten sollen unter X % vom Umsatz bleiben“ oder „nicht mehr als Vorjahr + Inflation“). Falls das prognostizierte Budget diese Ziele über- oder unterschreitet, muss eine Plausibilisierung erfolgen. Einerseits darf nicht unreflektiert gekürzt werden, da dies die Realisierbarkeit der Instandhaltungsplanung gefährdet. Andererseits ist ein modellhaft berechnetes Budget kein „in Stein gemeißelter“ Wert – es sollte von den Verantwortlichen überprüft werden, ob etwa Effizienzmaßnahmen vorgesehen sind, die Kosten senken könnten, oder ob Risiken bestehen, die höhere Rücklagen erfordern. Ein sinnvolles Vorgehen ist die Szenario-Analyse: Es werden Varianten des Budgets durchgespielt (z. B. Best-Case mit optimistischen Annahmen: wenig Störungen, Worst-Case mit zusätzlichen außerplanmäßigen Ausfällen). So gewinnt das Management ein Gefühl für die Bandbreite der möglichen Kosten und kann eventuelle Risikopuffer einplanen. Die Devise lautet: "Vom Überblick zur Detailbetrachtung" – zunächst die groben Budgetrahmen abstecken, dann iterativ in die Tiefe gehen und die Einzelansätze justieren.
Standortübergreifender Vergleich und Benchmarking:
Mit aufgestelltem Budgetplan pro Standort und Kategorie ergibt sich die Möglichkeit, die Budgets zwischen Werken bzw. Standorten zu vergleichen. Dies dient einerseits der Plausibilitätskontrolle und andererseits dem Best-Practice-Sharing. Wenn zwei Werke ähnliche Anlagen betreiben, aber deutlich unterschiedliche Instandhaltungskosten ausweisen, sollte die Ursache ergründet werden. Ein höheres Budget in Werk B könnte z. B. gerechtfertigt sein durch eine ältere Anlagenbasis oder höhere Produktionsleistung. Umgekehrt könnte es auch auf Effizienzunterschiede hindeuten – etwa unterschiedlicher Automatisierungsgrad in der Wartung, verschieden qualifiziertes Personal oder abweichende Strategien (reaktiv vs. präventiv). Identische Anlagen an unterschiedlichen Standorten bieten einen besonders aufschlussreichen Vergleich: Haben zwei Werke die gleiche Maschinenausstattung (z. B. identische Produktionslinie), so erwartet man eigentlich ähnliche Instandhaltungskosten. Weichen diese dennoch stark ab, lohnt ein genauer Blick: Vielleicht hat Werk A durch bessere präventive Wartung weniger Störfälle (und damit geringere Reparaturkosten), während Werk B mehr reaktiv repariert. Oder das Ersatzteilmanagement ist unterschiedlich (ein Werk verwendet günstig aufgearbeitete Teile, das andere nur Neuteile vom OEM). Solche Erkenntnisse sind Gold wert für das Asset Management: Sie zeigen Optimierungspotenziale auf und fördern einen internen Benchmarking-Prozess. Im Idealfall lernen die Standorte voneinander – das besser aufgestellte Werk dient als Vorbild, um auch im anderen Werk die Kosten zu senken, ohne die Zuverlässigkeit zu gefährden. Wichtig ist dabei immer, Rahmenbedingungen mit zu betrachten: Ein Standort in rauer Umgebung (z. B. Küstennähe mit salzhaltiger Luft) hat zwangsläufig höhere Instandhaltungslasten als ein Standort mit schonendem Umfeld – solche externen Einflüsse müssen im Vergleich berücksichtigt und kommuniziert werden (Dimensionskriterium „Umgebungsbedingungen“). Der standortübergreifende Budgetvergleich sollte daher qualitative Anmerkungen enthalten, die Unterschiede erklären (z. B. Alter der Anlagenflotte pro Werk, Umwelteinflüsse, unterschiedliche Produktvarianten, etc.).
Budgetkontrolle und präventive Optimierung:
Ist das Budget freigegeben und die Planperiode startet, beginnt die Phase der Budgetkontrolle. Hier geht es darum, Soll-Ist-Vergleiche während des Jahres durchzuführen und Abweichungen zu analysieren. Das Instandhaltungscontrolling überwacht monatlich oder quartalsweise, wie sich die tatsächlichen Kosten gegenüber dem Budget entwickeln. Größere Abweichungen werden untersucht: Handelt es sich um Timing-Verschiebungen (eine geplante Wartung wurde früher/später durchgeführt als angenommen) oder um echte Mehrkosten, etwa durch unerwartete Störungen? Besonders letztere sind kritisch und fließen in eine laufende Ausreißeranalyse ein. Tritt beispielsweise im ersten Quartal ein teurer Anlagenstillstand auf, so ist zu bewerten, ob dies ein singuläres Ereignis war oder ob eine Trendwende (etwa gehäufte Ausfälle) im Gange ist. Gegebenenfalls müssen Gegenmaßnahmen ergriffen werden – beispielsweise eine Sonderinspektion der betroffenen Anlage oder eine Anpassung der Wartungsintervalle –, um weitere Budgetüberschreitungen zu vermeiden. Hier zeigt sich die Verzahnung von Budgetkontrolle und Instandhaltungsplanung in der Praxis. Gleichzeitig liefert die Budgetkontrolle Feedback für die zukünftige Planung: KVP (kontinuierlicher Verbesserungsprozess) in der Instandhaltung. Wenn bestimmte Ansätze systematisch über- oder unterschritten werden, sollte die Planung methodisch angepasst werden. Nehmen wir an, mehrere Jahre in Folge wurde das Budget in der Anlagenklasse „Pumpen“ überschritten, weil es unerwartet viele Dichtungsschäden gab. Dann könnte man daraus schließen, dass die präventiven Wechselintervalle für Dichtungen verlängert werden müssen oder qualitativ bessere Dichtungen verwendet werden sollten – was wiederum mehr Budget für präventive Wartung erfordert, sich aber lohnt, wenn dadurch teurere Folgeschäden entfallen. Produktive, vorbeugende Instandhaltung gewinnt in diesem Kontext besondere Bedeutung: Die Budgetkontrolle macht transparent, wo reaktive Kosten dominieren, und ebnet so den Weg, diese durch gezielte präventive Maßnahmen zu senken. Untersuchungen bestätigen, dass präventive Instandhaltung erhebliche Einsparungen bringen kann, weil ungeplante Stillstandszeiten und umfangreiche Reparaturen vermieden werden. Anders formuliert: Die Instandhaltung steigert ihren „Wertbeitrag“, wenn sie Ausfälle verhindert statt nur zu reparieren. Daher sollte im Rahmen der Budgetkontrolle nicht allein auf die Einhaltung des Zahlenplans geschaut werden, sondern auf die Effizienz der Maßnahmen. Kennzahlen wie die Verfügbarkeit der Anlagen, die MTBF/MTTR (Mean Time Between Failures / Mean Time To Repair) und das Verhältnis von geplanten zu ungeplanten Instandhaltungsaufträgen liefern Hinweise, ob das eingesetzte Budget produktiv verwendet wird. Ein hoher Anteil ungeplanter Reparaturen trotz Budgetausschöpfung wäre ein Warnsignal – hier gilt es, durch verbesserte Planung und Wartung gegenzusteuern.
Ergebnisdarstellung und Dokumentation
Die Resultate der Budgetplanung müssen verständlich kommuniziert und dokumentiert werden. Für die Ergebnisdarstellung bieten sich Übersichts-Tabellen und Grafiken an, die die geplanten Kosten nach relevanten Kriterien aufschlüsseln.
Typische Darstellungen sind z. B.:
Budget nach Kostenarten: interne Personalkosten, Material, externe Dienstleistungen – um zu sehen, wohin das Geld fließt.
Budget nach Anlagenklassen: z. B. Balkendiagramm der vorgesehenen Kosten pro Klasse, um Hauptkostentreiber visuell hervorzuheben.
Zeitlicher Verlauf: ein Liniendiagramm, das die Ist-Kosten der Vorjahre und die geplanten Kosten der kommenden Jahre zeigt. Dies verdeutlicht Trends und Brüche (etwa Anstieg durch alternde Anlagen oder Abfall nach Ersatzinvestitionen).
Standortvergleich: eine Gegenüberstellung (wie Tabelle 1) oder prozentuale Anteile der Standorte am Gesamtbudget, um Unterschiede auf einen Blick erkennbar zu machen.
Wichtig ist dabei eine klare Gliederung und Beschriftung, da das Zielpublikum bereichsübergreifend ist – vom technischen Leiter bis zum Controller. Jede Zahl sollte in einen Kontext gestellt werden (z. B. „Werk B plant 1,63 Mio €, das sind 12 % mehr als Werk A, was hauptsächlich an höheren Aufwendungen für Pumpen liegt.“). Solche Erläuterungen ermöglichen es auch Nicht-Experten, die Kernaussagen nachzuvollziehen.
Neben den Präsentationsunterlagen empfiehlt sich dringend die Erstellung eines Begleitdokuments zur Budgetplanung. Dieses Dokument dient als Nachschlagewerk und zur Transparenz der Methodik.
Folgende Inhalte sollte es abdecken:
Datenstruktur und Quellen: Beschreibung, welche Daten aus welchen Systemen gezogen wurden (z. B. SAP-Transaktionen IW38 für die Auftragslisten), Stichtage, betrachtete Zeiträume, Wechselkurse falls relevant, etc.
Methodik und Annahmen: Erläuterung der Planungsmethodik (z. B. „Trendfortschreibung auf Basis 3-Jahres-Mittel, außer bei Anlage X, dort spezifische Schätzung wegen geplanter Revision“). Alle wichtigen Annahmen gehören hierhin: Preissteigerungsfaktoren, geplante Produktionsmengen, Lebensdauerannahmen, Verfügbarkeitsziele usw.
Klassifikationen und Kriterien: Definition der verwendeten Anlagenklassen (F-Klassen) und Kriterien. Beispielsweise ein Anhang mit Liste aller Anlagen und ihrer Klassenzuordnung, Altersgruppe, Kritikalitätseinstufung etc.
Auswertungsergebnisse im Detail: Während in der Präsentation meist aggregierte Charts gezeigt werden, kann das Begleitdokument tabellarische Detailauswertungen enthalten (z. B. vollständige Liste der Ist-Kosten je technischem Platz für die letzten Jahre, umfassende Pivot-Tabellen-Auszüge). Dies ermöglicht dem Controlling eine tiefergehende Prüfung bei Bedarf.
Maßnahmenkatalog: Falls im Zuge der Planung Optimierungsmaßnahmen identifiziert wurden (z. B. „Ölanalysen einführen für kritische Getriebe, um Ausfälle zu reduzieren“), sollten diese festgehalten und mit Verantwortlichkeiten und ggf. Budgetansätzen (Investitionsbudget für Verbesserungen) dokumentiert werden.
Genehmigungs- und Freigabehistorie: Zur Nachvollziehbarkeit kann man angeben, wann und von wem das Budget geprüft und freigegeben wurde, inklusive eventueller Anpassungen in Runden.
Dieses Begleitdokument stellt sicher, dass die Budgetzahlen nicht isoliert im Raum stehen, sondern mit ihrer Herleitung verstanden werden. Erfahrungsgemäß schätzen sowohl Instandhaltungsleitung als auch Finanz-Controller eine solche Dokumentation, da sie Missverständnisse vorbeugt („Weshalb ist Posten X so hoch? Siehe Dokument Kapitel Y für Begründung.“) und die Nachhaltigkeit der Planung erhöht. Insbesondere bei Personalwechsel oder im Folgejahr ist es immens hilfreich, die früheren Annahmen und Daten schnell rekonstruieren zu können.
Eine praxisorientierte Budgetplanung für die Instandhaltung erfordert fachübergreifendes Denken: Technische Kenntnisse über Anlagenzustände und Wartungsbedarfe müssen mit betriebswirtschaftlichen Methoden der Kostenanalyse und -prognose verknüpft werden. Durch die strukturierte Vorgehensweise – von der gründlichen Datensammlung über Pivot-gestützte Analysen nach technischen Dimensionen bis hin zur mehrjährigen Prognose unter Berücksichtigung von Alter, Nutzung und präventiven Maßnahmen – entsteht ein fundiertes Budget, das sowohl realistisch als auch strategisch ausgerichtet ist. Entscheidend ist, dass das Budget nicht als starre Begrenzung gesehen wird, sondern als Steuerungsinstrument: Im Planungsprozess werden wertvolle Insights gewonnen (z. B. welche Anlagen besonders kostentreibend oder störanfällig sind), die direkt in Verbesserungsmaßnahmen einfließen können.
Für die Instandhaltungsleitung bedeutet eine solche Budgetierung, Transparenz über die eigenen Prozesse zu gewinnen und gegenüber dem Management die nötigen Ressourcen plausibel zu begründen. Anstatt pauschal Kürzungen oder Aufstockungen zu diskutieren, können konkrete Zahlen und Analysen dargelegt werden – etwa dass ein gewisser Anstieg im Budget notwendig ist, weil präventive Instandhaltung ausgeweitet wird, was aber im Gegenzug das Ausfallrisiko senkt und indirekte Kosten spart. Controlling und technische Leitung erhalten mit dem beschriebenen Ansatz ein gemeinsames Verständnis: Die Instandhaltung wird plan- und messbar, Abweichungen werden systematisch erfasst und dienen als Lernkurve für künftige Planungen. Letztlich stärkt eine methodisch untermauerte Budgetplanung die Position der Instandhaltung im Unternehmen, weil sie zeigt, dass Instandhaltung nicht nur Kosten verursacht, sondern durch vorausschauende Planung aktiv zur Wertschöpfung beiträgt. Eine zuverlässige, gut gepflegte Anlage produziert qualitativ einwandfrei und ohne ungeplante Unterbrechungen – dafür bildet das Instandhaltungsbudget den finanziellen Rahmen, den es mit Sachverstand zu ermitteln und verantwortungsvoll einzusetzen gilt. Mit den dargestellten Methoden und Tools ist die Instandhaltungsabteilung bestens gerüstet, diese Herausforderung zu meistern, und das Unternehmen kann standortsübergreifend von einer optimierten, vergleichbaren und kontrollierten Instandhaltungsstrategie profitieren.